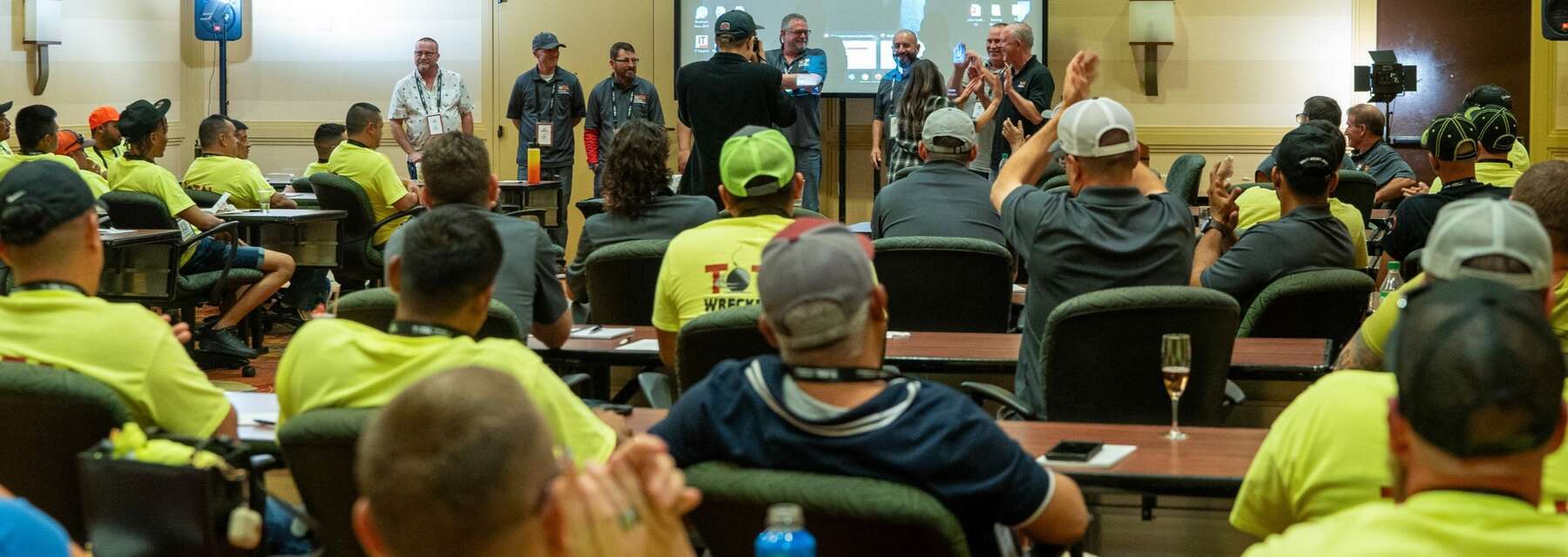
INTRODUCTION
For the past 10 years, Total Wrecking & Environmental has worked tirelessly to uphold the highest safety standards in the industry, ensuring that every employee on our jobsites is safe, informed, and accountable.
And we took our commitment to safety to new heights this year with our Safety Summit in Stone Mountain, GA.
This was far from your average training seminar; it was a full-company, three-day retreat where every member of the Total Wrecking team from across the country was flown in to immerse themselves in best practices and better get to know the whole team.
Total Wrecking’s most ardent mission is to ensure all team members, as well as their families, are of strong mental health, financially stable, and comfortable within all of their work environments.
This comprehensive summit was a testament to that steadfast dedication to care for your colleagues like they’re family.
THE SAFETY SUMMIT: A COMPREHENSIVE TRAINING EXERCISE
The summit was a multi-day, hands-on event that gave the whole Total Wrecking workforce the skills and tools needed to perform their work safely and efficiently.
The intent of the Safety Summit was, first and foremost, to provide necessary training directly related to the work that Total Wrecking performs, the hazards involved, and the steps and means to mitigate those hazards.
In other words, it’s about elevating awareness and empowering each person with a voice. Every member of Total Wrecking’s team needs to have the knowledge and skills they need to navigate the complexities of these inherently dangerous industrial demolition sites.
Total Wrecking firmly believes that everyone in the field should feel empowered to be a safety officer and to speak up or act when they see an opportunity.
Listed below are just some of the topics covered during the three-day summit:
• Lessons Learned: Discussing different events on a wide variety of job sites to better learn from past experiences.
• All-Stop Work Authority: Emphasizing the importance of every employee having the power and confidence to call an all-stop.
• Muster Points & Training: Ensuring everyone knows where to gather in an emergency.
• Situational Awareness: Training staff to be aware of their surroundings and potential hazards to avoid them more effectively.
• Environmental Health Hazards: Educating the team on potential environmental hazards and how to mitigate them, including:
– Asbestos Awareness
– PCB Awareness
– Lead Awareness
– Arsenic Awareness
– Cadmium Awareness
– Hexavalent Chromium
– Respirable Silica
• Respiratory Protection: Ensuring workers have the right equipment and training to protect their respiratory system from harmful contaminants.
• OSHA Focus 4: Addressing the four leading causes of fatalities in the construction industry: falls, struck-by, caught-in/between, and electrocutions.
• Fall Protection: Implementing specific safety protocols and procedures to prevent falls and ensure worker safety at elevated heights.
• Hazardous Waste Operations and Emergency Response: Training workers to safely handle hazardous waste and respond effectively to emergencies.
• Hazard Communication: Ensuring clear communication about potential hazards so every team member is informed and prepared.
• Emergency Action Plan: Ensuring everyone knows what to do in an emergency.
• Chain of Command: Clarifying the organizational structure and who to report to.
• Team Building: Strengthening the team dynamic and promoting a strong safety culture through communication and trust.
Frank & Sandy Bodami’s career-long dedication to the safety of his team has been paramount for the company, and its impact has been noticed within the industry. Above all else, he states his mission has always been to ensure every worker returns home safely at the end of the day.