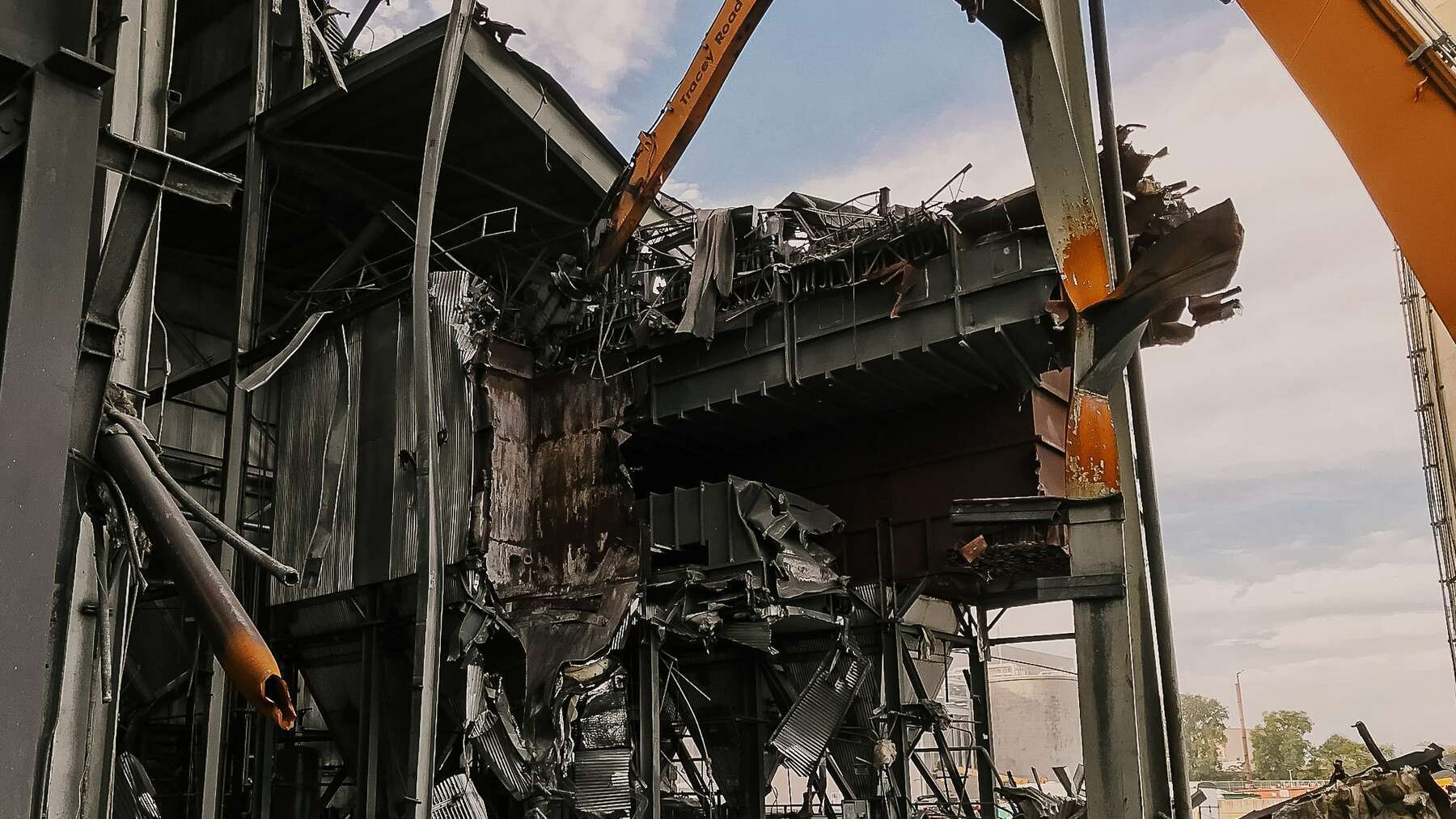
INTRODUCTION
Nothing is more important than safety, especially in an industry as hazardous as industrial demolition. By cementing the crucial need for constant, ongoing communication, protecting the community through detailed work practices, enforcing daily toolbox talks and hold points, enabling team-wide responsibility, and ensuring every employee has multi-dimensional training,
Everyone is responsible for safety. Whenever someone asks, “Who here is responsible for safety?” on a job site, it’s a trick question: everyone is! Of course there are people dedicated to managing it, including a Safety Director, who provides daily briefings, ensures paperwork is in order, and validates every employee’s training. But ultimately the responsibility falls on every single team member to protect the safety of themselves and those around them by having a questioning outlook that identifies weak or less thought-through details of a work plan.
COMMUNICATION IS KEY
Effective communication is absolutely paramount. Many of the daily activities on an active industrial demolition job site are extremely hazardous by their nature. In order to stay safe, ongoing communication and the detailed planning of daily activities are critical. This requires a process that is sustainable and repeatable over time.
Daily morning meetings and pre-job briefs, also known as “Toolbox Talks,” play a huge role in ensuring that roles and responsibilities are clearly outlined, everyone is on the same page, each and every person knows precisely what to do that day and understands what will be going on around them. They’re considered the most important 10-15 minutes of any work day. These crucial meetings are mandatory for all employees prior to work in an effort to validate that workers understand the scope of work as well as their individual roles and responsibilities.
These briefings are designed to engage employees in a discussion identifying potential hazards and how those hazards will be mitigated. When completed diligently and effectively, this process ensures everyone is prepared to perform their assigned work tasks safely and on a completely “event-free” site.
Communication is the most important part of maintaining a safe site but also the most challenging element to sustain. Things are constantly changing on an active site, meaning ongoing lines of communication need to be frequent and clear to keep up. People need to be in constant discussions about important questions, changing tasks, or new risks throughout the day to ensure no single stone goes unturned. Workers are specifically trained to have questioning attitudes so that every question is asked, every issue is addressed, and every task is considered from as many perspectives as possible.
HOLD POINTS
One element of industrial demolition job sites that encourages ongoing discussions are “stop gaps,” otherwise known as “hold points.” These are predetermined markers in the work day where workers will reconvene to discuss the next steps once a certain task or number of tasks are complete.
There are hold points for certain tasks that force pauses at certain points of the process to discuss critical pieces before proceeding. This could be air monitoring, another inspection, changing the type of personal protective equipment (PPE) being used by workers, or simply additional equipment. These are included in pre-task communications and built into procedures and Job Site Analyses (or “JSAs”).
The point is it not only facilitates communication, it forces teams to pause and recalibrate before transitioning to refocusing on a new, possibly more dangerous, task.
COMMUNITY PROTECTION
One of the primary reasons on-site safety is so vitally important is the protection of the communities that nationwide demolition contractors are serving.
Almost every industrial demolition project requires the removal of hazardous waste materials, which introduces a sprawling trucking element. Not only is it paramount that the right wastes go into the right place, but trucking routes and plans are also very sensitive. The project manager needs to determine a logical route that avoids traffic, small roads, residential areas, schools, and other areas to ensure that they’re not interfering with the community.
Dust migration is also a significant factor and potential threat to nearby communities. That’s why diligent nationwide demolition contractors will put stringent environmental control plans into place that limit dusting. Whether it’s extreme consciousness of the equipment or tools being used that can minimize dust or employing large foggers that use mist or fog to capture airborne particles, every precaution is taken to ensure site work stays exactly where it should: on-site.
Noise and view obstruction are more aesthetic, but equally important considerations to ensure work isn’t interfering with the community. Before a project ever commences, the competent demolition contractor will determine that the work will only be performed during normal business hours unless absolutely necessary. In addition, they’ll often install privacy and dust screens to cut down on site visibility, prevent bystanders, and mitigate the migration of dust.
IT’S A PERSONAL RESPONSIBILITY
“Stop work” ties into Total Wrecking’s foundational mantra that safety is a personal responsibility shared by the entire team.
At the core of “stop work” is the idea that everyone is comfortable and empowered to speak up if they have questions or concerns and to “stop work” on the site if they recognize a hazard. This isn’t simply an encouraged employee perk, but a powerful and vital responsibility to recognize and communicate a potential issue before someone gets hurt.
If that worker uncovers something that wasn’t discussed in the pre-project conversation, if something comes up that wasn’t proactively addressed, or if circumstances change that require a fresh discussion, they have full autonomy to put a “stop work” order on the site to address the new concerns. Nothing of potential concern should be brushed off and that’s a paramount aspect of Total Wrecking’s safety culture. Afterall, supervisors can’t monitor everything that’s happening at all times. Ultimately, the workers are the best and first ones to know and recognize the minute-to-minute hazards.
Another way that personal safety responsibility is encouraged is by promoting 3-way communication, where in loud environments things are asked or repeated multiple times by the speaker and listener to ensure everyone has a crystal clear and mutual understanding.
Additionally, a “lone worker” or “buddy system” policy that serves as another human performance tool within the industry. This ensures people aren’t working in dangerous environments alone, or at the very least not without a clear line of communication via cell phone or 2-way radio. These are common practices but many contractors don’t adhere to them day to day. Total Wrecking, on the other hand, uniquely and diligently enforces these stringent protocols and does not allow workers to perform any maintenance themselves.
THE TOTAL DIFFERENCE
Everything we’ve outlined is relatively standard practice within the hazard-prone industrial demolition industry. So, how does Total Wrecking differentiate themselves? The most obvious way they go above and beyond safety requirements is by strictly adhering to every single policy in practice, and setting the groundwork for each protocol up front to avoid delays, slow downs, and, most importantly, accidents.
Each and every Total Wrecking employee on-site is fully First Aid and CPR trained. OSHA requires that at least one on-site team member needs to be trained in these categories, and while some other contractors may have a handful or so on-site at any given time, Total Wrecking goes the extra mile by requiring every single person to be trained in this vein.
Total Wrecking is also proud of our adherence to our “Best Practices” category of safety measures, which include additional steps to protect their crews, the environment, and their communities. This includes practices like “dusting,” or the process of using Dust Bosses or Monsoons to mist the air and capture airborne dust particles. Dusting is an example of a measure that isn’t OSHA required but has proven to be effective at minimizing hazards and ensuring contractors are safe and kept well within compliance.
“100% fall protection” is another best practice of Total Wrecking’s that goes above and beyond OSHA requirements. This is the process of using two separate lines or tie-off points when working at heights, ensuring it’s virtually impossible for any height-related accidents.
TRAINING
Total Wrecking’s unique program is designed to ensure that our front-line employees and managers have the appropriate level of training to be successful and to allow industry best practices to be identified, recommended, and discussed in Safety Committees. They meet every regulatory and contractual requirement for training and enable peer-to-peer coaching opportunities that facilitate an exchange of information between individuals. .
Utilizing proprietary tracking,” Total Wrecking is able to ensure their employees are alerted as training qualifications reach their expiration date and require renewal. This software standardizes training for all employees and keeps track of who has what credentials, who needs to be retrained, and what certifications are about to expire.
Professional training within Total Wrecking is a step above the rest, encouraging and sometimes requiring safety staff to seek professional certifications for their positions beyond baseline requirements. Other employees will often gain additional certifications for specialty areas that may not be immediately relevant to their position but help offer them a more dimensional, and often more safe, foundation of knowledge.
CONCLUSION
At Total Wrecking & Environmental, “Total Safety” means empowering each and every employee to actively identify hazards, prevent and correct unsafe conditions, and demonstrate safe behaviors at all times. They accomplish these goals by setting clear expectations, holding all employees and management accountable for their performance, and providing extensive training, tools, and support needed.