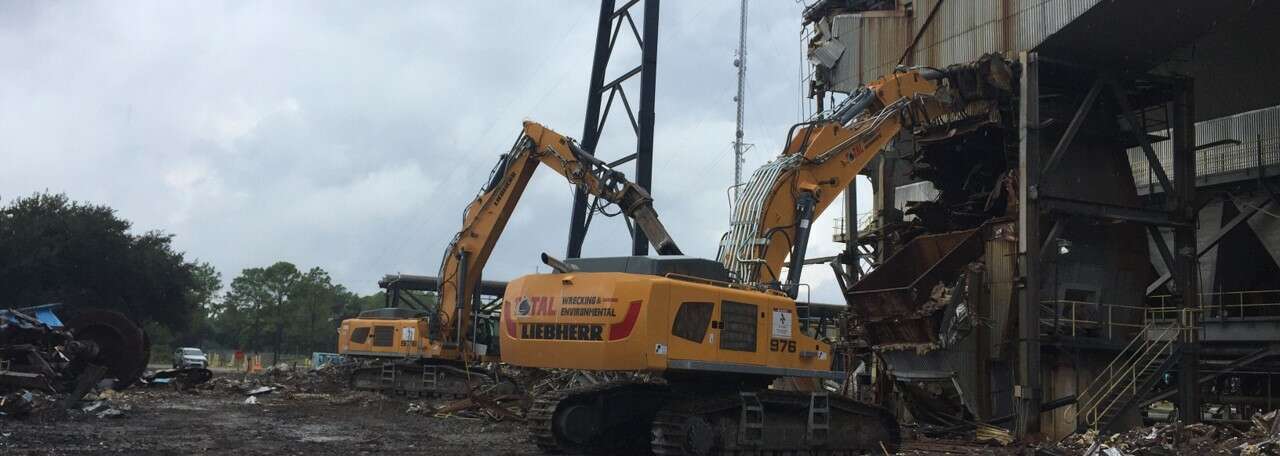
ABOUT THE COMPANY:
Since its construction in the 1950’s, the facility has experienced multiple leaks, and broken pipes in its heat transfer system resulting in the release of PCB-containing oil. This oil has, in turn, contaminated the surrounding concrete areas. Unfortunately APG inherited these challenges upon acquiring the facility, despite not being the cause of the original contamination. The challenging and highly dangerous project dealt with RCRA lead hazardous waste, widespread TSCA level PCB contamination, and Category I non-friable asbestos waste, all of which fall under stringent regulatory requirements for demolition, transportation, disposal, on-site storage, and employee exposure management. To add to the challenge, all of Total Wrecking’s work takes place within an active manufacturing plant. While demolition was underway, manufacturing processes continued in the attached buildings and surrounding areas, along with active rail tracks within the facility. Although Total Wrecking has successfully completed other, often larger, projects with the same elements for clients like General Electric, every project presents unique challenges due to different layouts and manifestations. Phase one is expected to take approximately 10 months, with phase two being a six-month undertaking, likely to begin in early 2024.
THE CHALLENGE:
The manufacturing building itself is a humongous, 5-story structure that takes up the space of two football fields. The heat transfer piping system containing PCB oils within it stretches for over 10 full miles and PCB contamination of concrete existed on every single floor. One of the main issues at the facility is its elaborate and highly sensitive heat transfer system, which maintains the delicate temperature of its manufactured products. This closed system contains both boilers and piping with PCB containing oil that circulates in order to heat products. In the early 1980s, this section of the site underwent a change whereby the PCB oil in the system was drained and replaced with T-66 oil. However, residual PCBs remained trapped within the piping, and adhered to the inner walls in a tar-like consistency. In addition to PCBs, Total Wrecking also managed asbestos containing mastic on precast concrete roof panels, which had to be segregated from other debris which was being processed into pieces six inches or smaller in order to be disposed of in a TSCA permitted landfill. Processing Category I non-friable asbestos-containing material changes it’s regulatory status from non-regulated to regulated asbestos, meaning any concrete panels with asbestos had to be separated from the rest of the building and carefully disposed of without further processing. Asbestos was also detected in gaskets between pipe flanges, requiring pipe joints to be cut on each side and disposed of with the asbestos gaskets still intact. Other interconnected buildings were constructed after original site construction and shared exterior walls with the manufacturing building Total Wrecking was tasked with taking down. That meant that each part of the building needed to be carefully separated from the structure being demolished to avoid damages and allow neighboring operations to safely continue without interruption. The APG facility also contains multiple active sets of rail spurs to transport both raw materials and finished products in and out of the site on railcars and tankers. This fully-active component adds another element of complexity to the demolition process that demo professionals had to plan around and safely navigate throughout all of their work.
THE SOLUTION:
The multi-phase project at APG involved a long list of chronological steps, starting with the capture of all remaining oils within the extensive 10-mile piping system. Total Wrecking’s services kicked off in November 2022 with the specific goal of removing all oil from pipes containing PCB residuals throughout winter and before temperatures rose. The PCB contaminated T-66 oil had unique characteristics, solidifying into a tar-like consistency at cooler temperatures but liquefying when heated. Oil collection and pipe removal had to be very carefully timed to prevent additional leaks when the weather became warmer. Total Wrecking’s demolition, abatement, and remediation experts then proceeded to carefully dismantle the building and brought all materials down to the concrete slabs at grade, which were to be addressed separately in Phase II of the Project. Total Wrecking’s expert remediation project managers helped develop time and motion studies, and comprehensive cost analyses to help APG choose the most cost-effective method(s) for remediation and demolition. Another incredibly important project component was the prevention of cross-contamination, allowing for salvaging and recycling of the uncontaminated structural steel, which had the potential to generate upwards of $3 million worth of shared revenue between Total Wrecking and the Owner. Before any demolition took place, Total Wrecking had to address a number of hazardous material issues, including block walls and structural members with loose and peeling lead-based paint that had to be scraped off and carefully collected. If not removed, any contaminated material had to be disposed of as RCRA hazardous waste, which when combined with the TSCA waste stream presented limited options for the combined RCRA/TSCA waste disposal. As with any demolition project, unforeseen challenges did arise, including the presence of residual oil in the pipes, even though the system had allegedly been drained by the Owner before the project started. Because landfills cannot accept TSCA waste containing free liquids, debris with free liquid could seriously jeopardize the ability to properly dispose of waste. Thankfully, Total Wrecking was able to identify and remove all remaining oil in the pipes that posed the risk of contaminating remaining materials, avoiding a potentially costly mistake.
THE RESULTS:
Total Wrecking was instrumental in helping APG define a comprehensive demolition timeline, as well as a performance-based disposal plan, which involved disposing of everything based on the original concentration of the PCB source during Phase I, and final remediation and disposal in Phase II under a self-implementing clean-up plan. Months of careful planning involved had helped ensure that the sensitive management of all materials prevented any further contamination and allowed for all debris to be disposed of safely, efficiently, and cost-effectively, and allowed for the harvesting of millions of dollars worth of uncontaminated scrap metals to help the Owner pay for the project. Remediation experts at Total Wrecking had spent five months removing trapped oils within the piping system and strategically removing sections of pipe most likely to contain residual T-66 oil. As they surgically dismantled the 5-story manufacturing building, ensuring all waste streams were safely segregated, they also ensured that every shared wall remained intact and undisturbed so that active and neighboring operations could continue without interruption. Despite the monumental hurdles posed by widespread PCB contamination, asbestos, and lead-based paint, Total Wrecking had successfully navigated the complex regulatory environment and developed innovative solutions that minimized costs and, most importantly, ensured the safety of everyone involved. With a keen understanding of project-specific nuances and a steadfast dedication to maintaining the highest standards of demolition excellence, Total Wrecking stood out as the go-to choice for power plant owners, building managers, engineers, and industrial demolition professionals looking for an all-in-one contractor to safely, efficiently, and expertly manage every aspect of their demolition project.
“I appreciated the ease in dealing with the Total Wrecking team, both in the field and Administratively. Total Wrecking’s willingness to accommodate changes and overcome unseen challenges kept the project running smoothly. The manner that they operated in was safe, effective and efficient. Quandel Construction would like to express our confidence in Total Wrecking and our desire to work with their team on future projects.”
Shawn Edmonds
Project Superintendent , Quandel Construction Group